Quality Check: In which condition are your pneumatic tube carriers?
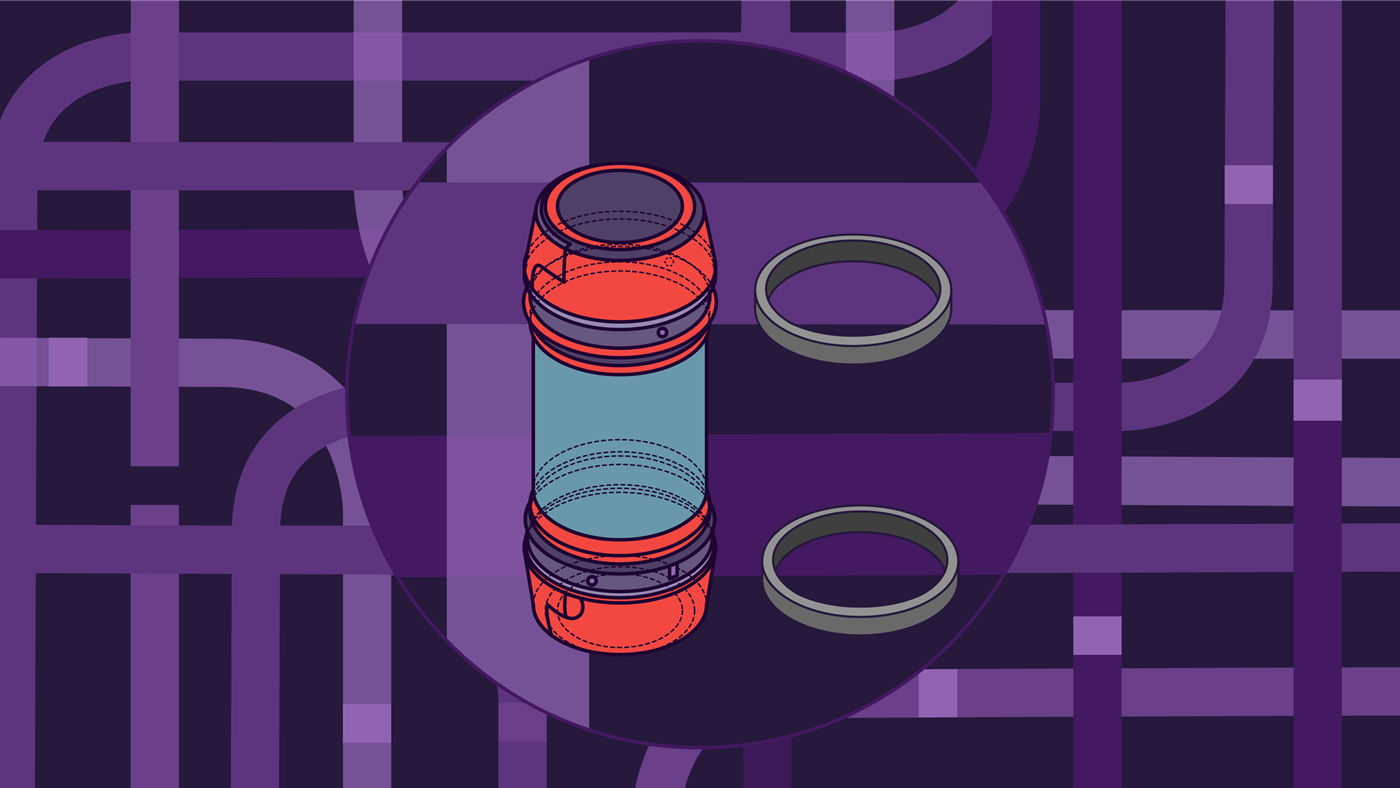
You cannot omit the pneumatic tube system from the daily routine of medical staff. Numbers of carriers that relentlessly transport critical goods between wards, laboratories and the central pharmacy are the heart of every system. With a length of 33 cm and a diameter of up to 16 cm, carriers can travel up to 6 meters per second; one carrier can transport a weight of almost 2 kilograms. The goods can be visually checked through the transparent, impact resistant and unbreakable plastic body. Besides, colored caps enable a customizable categorization system, for example, according to the carrier content, the urgency or the hospital department.
Thanks to an RFID transponder (radio-frequency identification), the carriers can be easily returned to the system after emptying and be sent back to their home station. Alternatively, a system-controlled empty carrier distribution can be used: the system recognizes the greatest need for empty carriers and distributes them accordingly. This ensures that all stations are continuously supplied with a sufficient number of carriers.
What happens if carriers are not in perfect condition?
Every hospital is different; hence, the planning of each pneumatic tube system is individual. However, they have one thing in common: high quality standards must be guaranteed to ensure safe transport of medical goods. To assure medical goods are safely moved from A to B, it is strongly recommended to regularly check whether
- both Velcro rings are in a proper condition for smooth transportation,
- all closures on a container’s opening mechanism are positioned correctly in the hinges, and
- protective materials like foil pockets are available and intact.
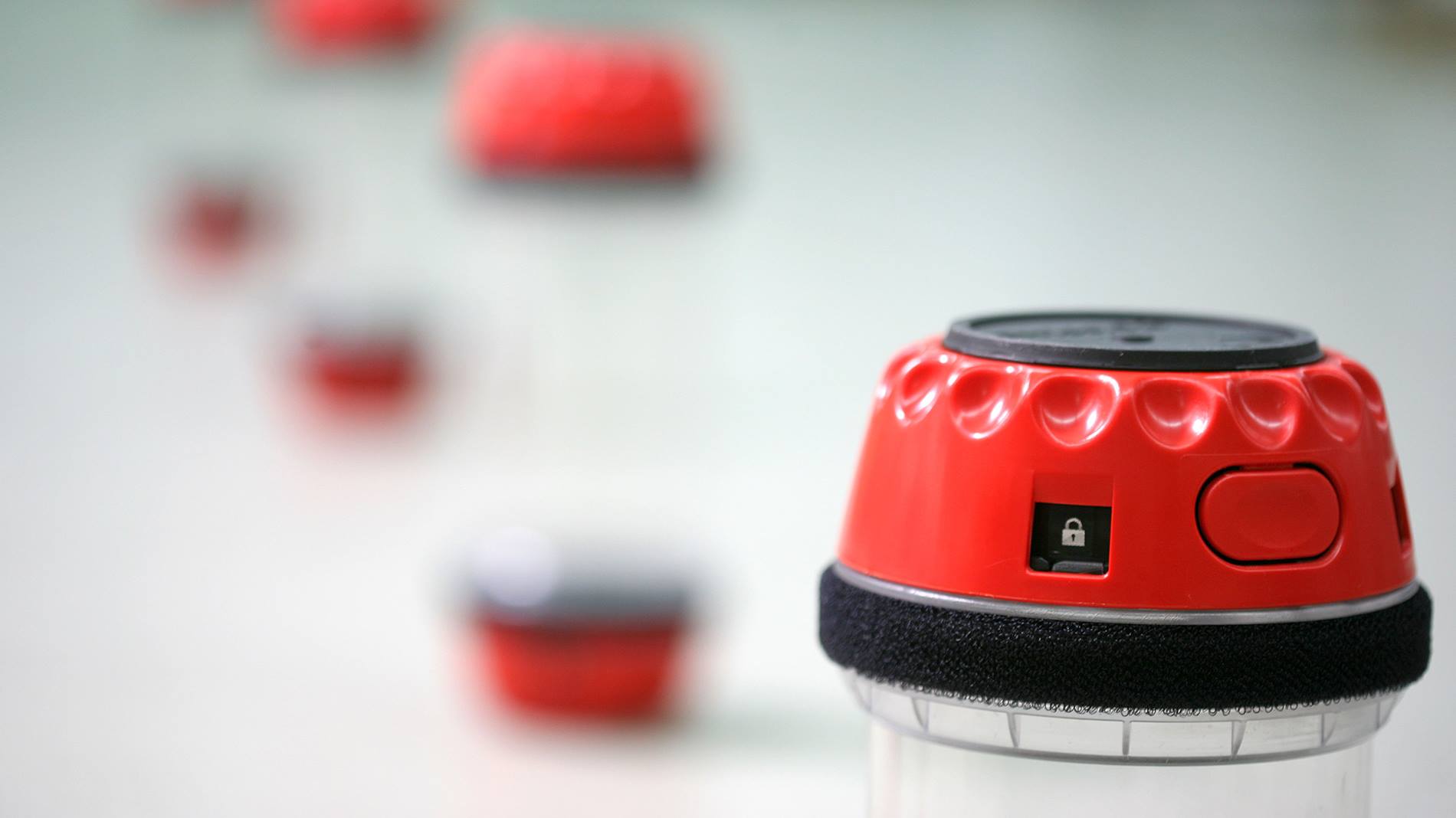
When parts wear out, the full quality is no longer given. This can cause spilling of substances from the carrier into the tubes. In the worst case, the carrier may even open during transport.
Once the Velcro rings of a container have worn out over time, the pneumatic transport is negatively affected. This wear and tear can lead to friction inside the tubes during a journey. Another problem may be that the carriers arrive too fast at the recipient stations. Additionally, the seam on the Velcro rings must be checked regularly to avoid accidental detachment of a ring. This also avoids the need to remove the Velcro rings from the tubes afterwards.
In case of signs of abrasion, the rings need to be replaced. After 1,000 runs, it is recommended to use new Velcro rings at the latest. However, depending on the used tube material and also the distance covered by a carrier, the number of maximum transports may be lower. This is why, the carriers need to be regularly checked for signs of wear.
In addition to the rings, the opening and closing mechanism should also be checked regularly to prevent unplanned openings during transportations.
In order to extend the lifetime of a container and of course also to fulfill the prescribed hygienic regulations, used carriers should be cleaned on a regular basis. Special cleaning machines take care of this. This way, contamination can be avoided.
Due to the intensive, daily use of pneumatic tube systems in a hospital, contamination can also occur inside the pipes. On the one hand, this may happen due to wear or friction, if maintenance is insufficient or not done. On the other hand, this may also cause by the deposition of dust or liquids in the system. A cleaning carrier can be used to clear the insides of the tube and remove dirt and contaminants. The sponges of the cleaning carrier can be easily replaced after use. By using suitable cleaning products, it can be ensured that the pneumatic tube components are not negatively affected.
Carrier management – keep an eye on the condition of your carriers
Hospitals that automate their transport with a TranspoNet pneumatic tube system are capable of sending up to 350 carriers through the system at peak times. In order to be able to track the condition of the individual carriers, a software-based carrier management is necessary.
Stocks can be managed easily and reliably via the TranspoNet pneumatic tube control software. The carrier management records to which home station a specific container belongs, as well as the total number of carriers at a station. Additionally, the software tracks how many transports a specific pneumatic tube carrier has made so far, which serves as a reference for the condition of the individual carrier. After maintenance service, the counter can be reset in the software.
In general, the life cycle of a carrier depends on the degree of use. Five years after initial operation, a carrier should be replaced.
Contact us. We will help you to ensure your pneumatic tube carriers are in perfect condition.